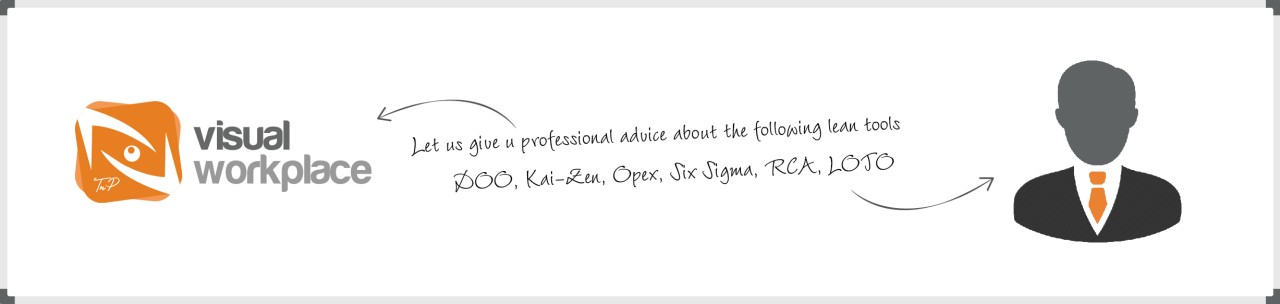
Various lean improvement tools | Visual management boards
Below is a brief description of the other lean methods. For each method, we have an application; read more below or contact one of our employees and let us advise you.
The daily performance review (DPR)
The daily performance review. The daily performance review has three objectives:
- Performance review
- Escalation and handling of deviations
- Continuous improvement
Performance review
During the daily performance review, representatives of a process meet at a fixed time to account for the KPIs (Key Performance Indicators). This is often done using a visualisation board.
Escalation and handling of deviations
In the daily performance review, all deviations from a process that cannot be resolved by the representatives are discussed. By requesting support from a supporting department in a structured way, the status and the action plan is clear to everyone in the organisation.
Continuous improvement
A result of this review and escalation process will provide insight into the hidden improvement potential. A multidisciplinary approach with a structured problem solving method approach (PDCA, DMAIC) will result in continuous improvement of processes.
The daily performance review must be supported by excellent visualisation. TnP Visual Workplace can help in this as a partner. Please contact us for more information.
Kai-Zen (Kaizen method)
Kaizen is Japanese for "change to better" or "improvement" and is an approach of productivity improvement. The Toyota Production System is quite well known for its kaizen. Toyota expects its employees to take the initiative to stop the production in the case of deviations and to subsequently work on improvement together with colleagues and supervisors. The cycle of Kaizen method can be defined as:
- Standardise an activity
- Then measure the standard activity (cycle time / inventory)
- Check the measuring method for accuracy
- Improve the activity
- Standardise the new way of working
- Start the next Kaizen cycle
A better definition of the Japanese usage of the Kaizen method is "disassemble to reassemble in a better way." The thing that gets disassembled is usually a process, a system, a product or a service. Kaizen is a daily activity with a purpose that goes beyond improvement. It is also a process that, when done correctly, makes the workplace more humane: it eliminates hard work (both mentally and physically), and it teaches people to see the waste in a process and to eliminate it.
Opex (Operational Excellence method)
The concept of operational excellence comes from the book "The disciplines of market leaders" written by Treacy and Wiersema. It describes three pillars for a well-functioning enterprise: customer intimacy, product leadership and operational excellence. The operational excellence is the realisation of a distinctive market position by delivering products and / or services with excellent operating performance reflected in aspects such as low pricing, reliable delivery and good service. Operational excellence focuses on reducing operational costs.
Six Sigma
Six Sigma is based on statistical thinking and has its origins in the quality circle by Deming (PDCA, Plan-Do-Check-Act). In addition there is a fixed methodology used to solve problems, the DMAIC method. DMAIC is an acronym for Define Measure Analyse Improve Control. DMAIC is generically applicable in every business. Six Sigma has a crystallised infrastructure with task forces. Six Sigma is seen by many as a continuation of existing management methods, which is often based on Statistical Process Control (SPC) as the underlying approach.
DMAIC and Six Sigma visualisation boards
Visualising a Six Sigma process is an important step in the work of the Six Sigma teams. Through visualisation, both the participants of the Six Sigma processes and the employees get involved in the improvement processes. Visualisation can be done using a DMAIC board (Define Measure Analyse Improve Control). An example of a DMAIC board is shown in a picture on the right. On the DMAIC boards the information from the various steps is presented by magnetic windows or magnetic ring binders.
RCA (Root Cause Analysis)
In a Root Cause Analysis an error or problem is incrementally analysed by going back to the root causes that caused the problem. By using a cause-effect diagram, causes are mapped out. Only when a clear overview is mapped of the root causes can actions be planned to address the root causes. These actions prevent similar problems in the future.
Visualisation is a powerful tool to get to the root cause. TnP Visual Workplace supported many customers in their problem solution structure. This may be by means of improvement boards, PDCA / DMAIC boards, but also by providing visualisation boards with a fishbone diagram (Fishbone) or A3 problem solving cards / visualisation boards.
To the root cause: 5 times why. A technique to find the root cause is "5 times why". With regard to a consequence, you ask why it has been caused. The cause that you will find is a result of something, so you ask again, why it has been caused. After questioning this about 5 times you get to the root causes. These are the causes that you can address, to avoid similar problems.
These root causes often result in multiple problems and therefore addressing the root causes is usually very rewarding.
LOTO
Visualisation plays an important role in the overall process of a LOTO strategy. From visualising the basic steps, visualising the LOTO locks and the LOTO board to, of course, the mapping of the LOTO procedure
Why LOTO
Inadequate procedures for control of hazardous energy are the main reason for accidents. A typical case occurs when employees restart the machine, and they are not aware that maintenance operations are still being performed. Accidents also take place because there is still potential energy in the machine after it is separated from the power source. An effective means of safety management, with regard to the control of energy, is the application of a suitable Lock Out, Tag Out-procedure (restart lockout / tag, LOTO).
What is LOTO? LOTO stands for Lock out Tag Out
The purpose of LOTO is to increase personal safety when performing work! It should also ensure that no hazard / risk is posed to others or the machine. This is done by releasing energy and keeping machinery / equipment energy-free (yourself) (by hanging locks - in-house key management). "Energy" forms include: steam, electricity, compressed air, springforce, laser light, oil pressure, gravity, temperature, product or the supply or drainage of raw materials.
When do we use LOTO:
- If (rest) energy can endanger yourself, others or machines.
- If there is an increased risk (working on the same machine with more than one person).
- In the event of doubt.
- Technical intervention. Changing the design, in which tools are used, components are disconnected. Standard safety features no longer suffice. LoTo is required.
- If a consequence is very serious.
Always when working on equipment where, in the event of an incident, the consequences can be very serious. Visualisation plays an important role in the overall process of a LOTO strategy. From visualising the basic steps, visualising the LOTO locks and the LOTO board to, of course, mapping the LOTO procedure.